What is flame retardant cable?
In building construction, electrical cable sheathing is a potential source of fuel in the event of a fire. Soft-skin flame retardant cables consist of single or multi-stranded conductor cores (copper), individual core insulation (polymer) and an outer insulating sheath (polymer). This arrangement has a continuous operating temperature of 80°C. Because this arrangement contains polymers that easily burn, soft-skin cable manufacturers may use LSF (Low Smoke and Fume) or LSZH (Low Smoke Zero Halogen) fire retardant polymers to limit the spread of fire along the sheathing. Halogens (non-metallic elements) are added to the outer sheath such as; chlorine, bromine and fluorine. When exposed to a fire, these halogenated polymers will release halides which are extremely toxic. The outer and inner sheaths of soft skin polymer cables burn and contribute to a fire releasing toxic smoke which can itself ignite, often explosively. Further and crucially, in the event of a fire flame retardant cables offer little benefit with regard to maintaining circuit integrity.
Fire Resistant cables differ from flame retardant cables in that they are designed to maintain circuit integrity and continue working during a fire…
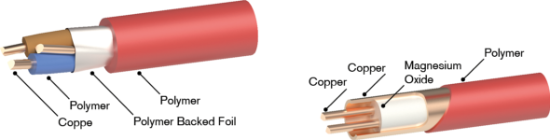
What Is Mineral Insulated Cable?
The acronym MICC stands for Mineral Insulated Copper Cable. Mineral Insulated Copper Cable is an example of Fire Resistant cable; it neither release toxins, nor will burn. Unlike soft-skin polymeric cable, MICC utilises just two unique elements, copper and magnesium oxide. It consists of single or multiple conductors (copper), core insulation (highly compressed magnesium oxide) and an outer copper sheath (copper). This unique composition and arrangement of just two materials has an outer melting point of over 1000°C (the melting point of copper) and ultimately 2800°C for the insulation (magnesium oxide). A bare mineral cable can work continuously up to 250°C.
What is the main advantage of MICC Cable?
The metal sheath and solid filling of MI cable makes it mechanically robust and resistant to impact; an MI cable may be struck repeatedly with a hammer and still provide adequate insulation resistance for a circuit. The combination of an aluminium oxide insulation and copper outer sheath is the key to MICC's fire survivability. The increased continuous and maximum operating temperature of MICC ensures mineral cable can safely carry a load under temperatures in excess of 1000°C making it a true fire survival cable. Mineral Cable is water and oil resistant, can carry greater current ratings, requires no conduit for mechanical or vermin protection, is UV and radiation resistant and can last well in excess of 50 years.
- Fire Resistant: Mineral insulated cable can work at a continuous ambient temperatures of up to 250°C, up to three hours at 950°C in a fire situation and even up to 1083°C for shorter periods. It will neither burn nor support combustion. The non-flammable copper sheath and insulation resists the transmission of vapours, gases and flame between items of equipment connected by the cable and will resist fire conditions longer than the enclosing .
- Mechanical strength: The outer copper sheath provides a protective barrier, providing extreme protection against mechanical stresses that would be fatal to conventional soft-skin cables. It is highly resistant to twisting, bending and will even continue to provide circuit integrity where the cable is almost completely flattened.
- Waterproof: The protective barrier created by the outer copper sheath combined with ATEX approved fittings and terminations make an MICC connection completely impervious to ingress from water, oil and gases. MICC is suitable for indoor or outdoor applications or for installation under concrete.
- Ease of Use and Cost: Mineral Cable is fully annealed and consequently extremely ductile and easily manipulated to following existing wiring routes and irregular shapes. Testing has proved that Mineral cable can fitted in a shorter time than soft-skin along with conduit. See timed and costed installation comparison here https://www.youtube.com/watch?v=59k7dQNMQv0.
The total life cycle costs of MICC in a building with a typical 40-50 year design expectancy is considerably lower than XLPE steel wire armoured LSZH fire retardant cable, thus off-setting any additional initial expenditure.
For the majority of modern installations, bare copper sheathed cable is sufficient and requires no additional outer covering. In this state the cable is resistant to oil, water and many other naturally occurring gases and liquids. Bare mineral cable is preferable for use in historic and listed buildings, such as castles, where the natural darkening of the copper due to oxidation causes it to blend in with stonework. Corrosion resistance makes mineral insulated cable ideal for use in areas where failure and replacement could be dangerous or even impossible. For example, Mineral insulated cable is used in nuclear plants to monitor core temperatures. Where the natural corrosion resistance of the copper sheath is not sufficient for instance in chemical processing facilities it can be augmented with an additional LSZH (Low Smoke Zero Halogen) outer coating. This outer coating can also be used for coloured circuit identification or visual appearance.
What Are Mineral Insulated Cables Used For?
Mineral Insulated cables have been designed specifically for critical and life saving systems where continuity is required in the event of a fire. They are specified for a wide variety of applications, from emergency lighting and fire alarm systems to instrumentation for nuclear reactors and industrial processing. For the question is pyro cable still used, the answer is a resounding yes!
A brief outline of where MICC cable is used:
* Emergency Lighting & Fire Alarm Systems
* Fire Detection and Prevention Systems
* Sprinkler Systems
* Public Address Systems
* Lifts & Escalators
* Stop/Start Controls
* Multi-Storey Car Parks
* Airports
* Hospitals
* Shopping Centres
* Churches, museums and other Listed and historic buildings
* Petrol Station Forecourts
* Hotels & Catering
* Nuclear Power Stations
Approvals and Standards
Mineral insulated cables are designed to meet some of the most stringent real-world derived tests around the world. Our cables are installed in some of the worlds largest and most important buildings and recognised throughout the electrical industry as the best choice for fire survival. The quality and reliability of our mineral insulated cables meet and exceed British, European and Australian standards and maintain certifications from BRE-LPCB, Warrington Fire Research Centre and London Underground with our termination glands approved by SIRA-ATEX EExd. Our mineral cable approvals include:
* British fire performance standards BS En 50200 PH120 Enhanced demands 2 hours fire resistance at 850°C
* BS 5839-1 Enhanced to BS 8434-2
* BS 6387 category C, W & Z demands that cables perform safely for 3 hours at 950°C
* AS/NZS 3013
For a full outline of our approvals and description of the relevant standards please see the following linked pdf. [LINK]
History
Finally a short history. Originally patented by Swiss inventor Arnold Francois Borel in 1896 and produced commercially in France in 1932. Mineral insulated cable was installed on large marine vessels such as the SS Normadie, oil tankers and also historic buildings such as the Louvre museum. In 1937 patents were secured by British companies and UK production began shortly thereafter. Mineral cable was produced extensively during the Second World War with a focus on military applications. To date, mineral insulated cable has been continuously manufactured in the UK for over 80 years.
Remora Electrical is proud to uphold that long-standing tradition by continuing to supply a 100% UK manufactured product.